Vibration Testing Fully Connected Cars
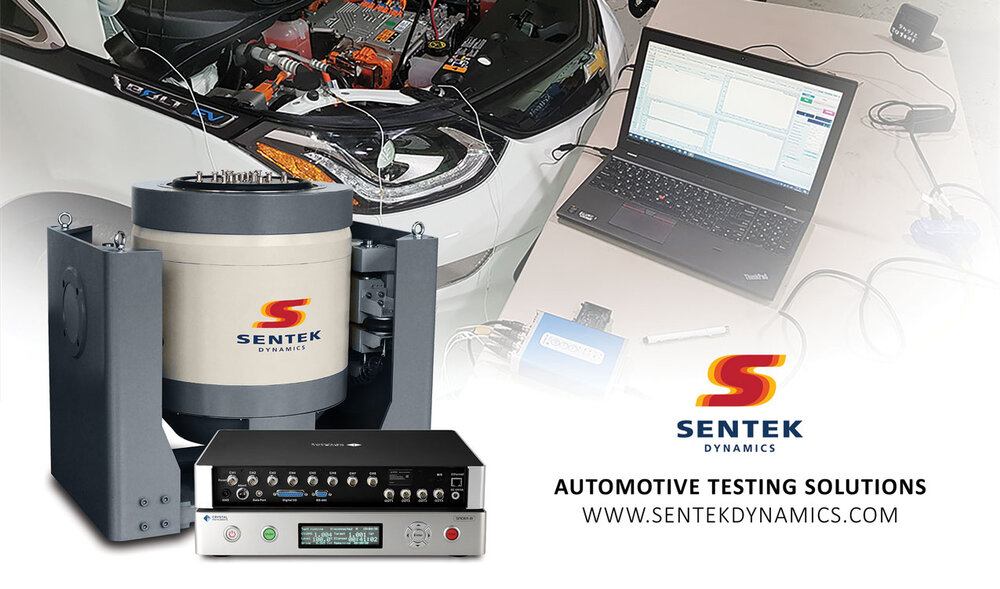
Vibration testing of automotive components helps manufacturers ensure both a sound design and improved reliability. The current growing demand for electric vehicles has placed battery testing into the spotlight and as a result, attention for vibration tests of electric vehicle batteries has increased. New advancements in testing electric vehicle batteries requires CAN bus signal monitoring of the batteries’ internal memory while undergoing a vibration test. Monitoring CAN bus signals during a test is certainly not a new idea. However, CAN bus signal monitoring while running a vibration test is a recent development driven by smart battery designs featuring internal controls for heading, voltage monitoring, and feedback capacity.
Testing non-electrical automotive components is fairly routine and well understood. Companies can test for a variety of mechanical conditions including fatigue damage and mode shape identification. Electrical components, which are growing in number within newer cars, may require all the same mechanical tests while also including electronic performance as an equally critical factor to monitor.
Crystal Instruments utilizes the Spider-CAN (CAN bus) to monitor electrical signals sent from automotive components directly through the Spider-81. This may not seem highly impressive since many companies can monitor CAN bus signals with the use of a separate CAN bus USB adapter such as the CANable or PCAN adapter. However, the Spider-81 vibration controller’s advantage is its ability to collect CAN bus signals and provide feedback based on those signals.
One such example might include a battery test with an overheat condition. The Spider-81 vibration controller uses CAN bus signals to stop or lower the vibration level if a battery is registering an overheat condition. Crystal Instruments’ vibration controllers not only register such readings but can also act in reaction to those readings by lowering the vibration level or stopping the test altogether.
Obviously, there are many permutations of this type of smart logic and closed loop feedback for fully connected cars. As autonomous vehicles increase in mainstream popularity, the challenges in vibration testing automotive components also increases despite a lack mechanical failures to prevent failure while components are being vibrated during a representative road condition.
Providing testing capabilities for tomorrow’s problems is what Sentek Dynamics sets out to accomplish. Shipments of complete systems from our North Carolina facility are available now:
Affordable contract testing services are available at our North Carolina testing lab. Contact us for more information.